Encirc Beverages' shift work story
How this manufacturer transformed its shift planning approach with optashift
Optimising shift pattern design
In this customer story you’ll learn how Encirc Beverages and optashift developed an innovative and highly-collaborative annual shift pattern design process.
The new approach is delivering significant and sustainable positive impacts for both Encirc Beverages and its shift workers.
A detailed shift work case study follows the summary below.
Table of Contents
Summary
Industry
Food and Beverage Manufacturing
(bottling, warehousing and distribution)
Challenges
- Complex demand profile
- Shift worker frustration with shift patterns
- Potential for disruption to employee work-life balance
- Un-optimised distribution of shift pattern features across teams
- Challenging time-pressured annual shift planning process
Solution
- Assessment and conversion of capacity plan to shift patterns and crew structures
- Collaborative shift pattern design process using unique governance framework, tools & approach
- High levels of Trade Union/employee engagement & communications
- Robust pan-stakeholder change management project processes
Outcomes
- Shift patterns optimised to demand & employee preferences
- Resource model underpinning productivity & service levels
- Balanced & fair annual shift calendars
- Well-received engagement & co-design process that’s helped improve management-Trade Union relations
- Shift planning framework established that underpins responsiveness, resilience and continuous improvement
- The initiative secured an Innovation & Collaboration award as recognition for its impact and success
The ‘Who’ - A dynamic industry leader
Encirc, a Vidrala Group company, has established itself as the UK’s leading wine, beer and spirits bottle producers and fillers.
It enjoys a 40 per cent market share and bottles 18 of the top 20 wine brands in the UK.
The Park is the business’ highly advanced, sustainable and award-winning manufacturing facility in Avonmouth near Bristol.
The site employs over 400 people and provides bottling, warehousing and distribution services.
Encirc’s vision is ‘Great People, Great Place and Great Future’, which focusses on three fundamental strategic pillars to underpin business growth – the value of employees, workplace facilities, culture and protecting the natural environment.
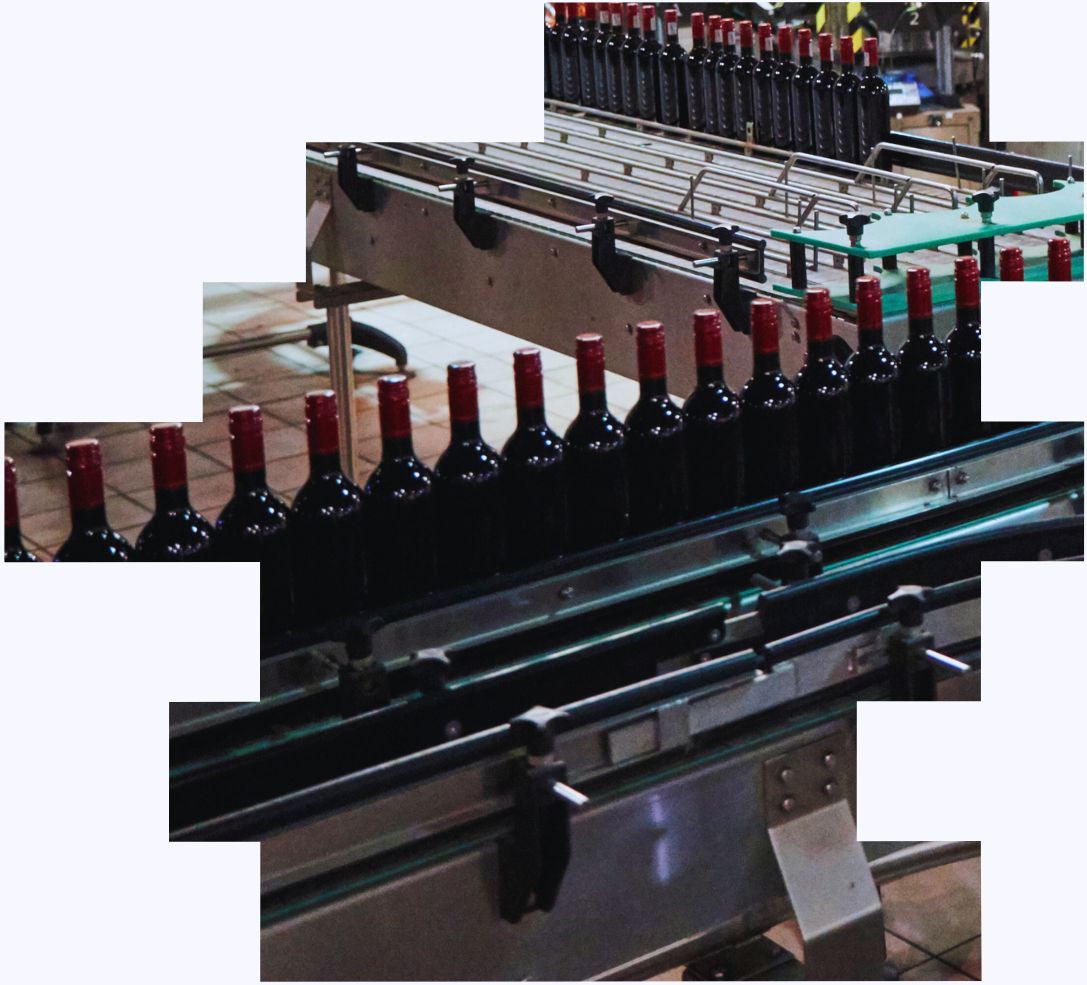
Shift Work Assessment
Optimising shift patterns and shift work delivers huge benefits…but complexity and competing priorities sees many organisations leave things as they are.
Our Shift Work Assessment is a streamlined process which quickly analyses all relevant operational and HR factors to give you a tailored plan for immediate improvement.
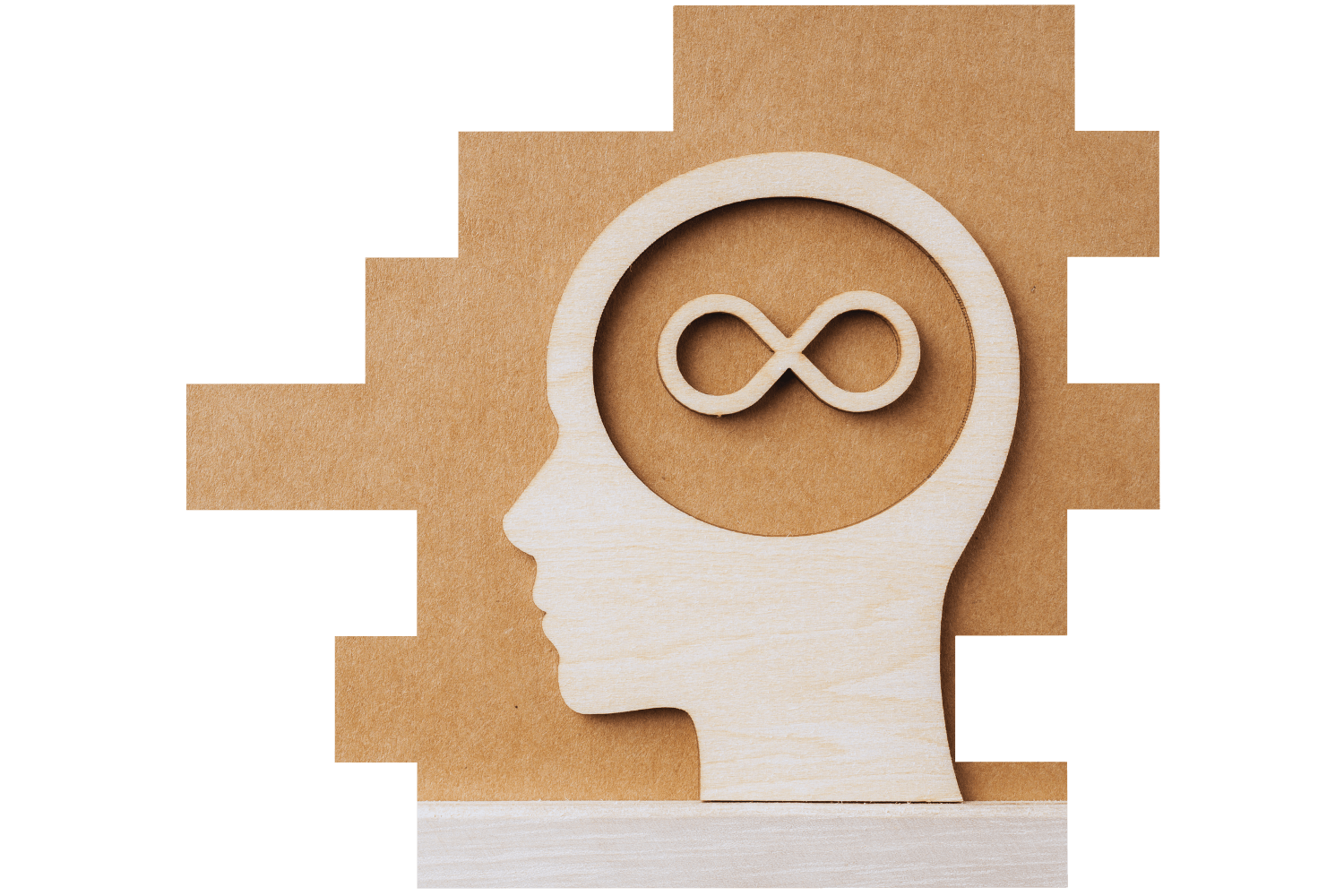
The ‘What & Why’ - Common shift planning challenges
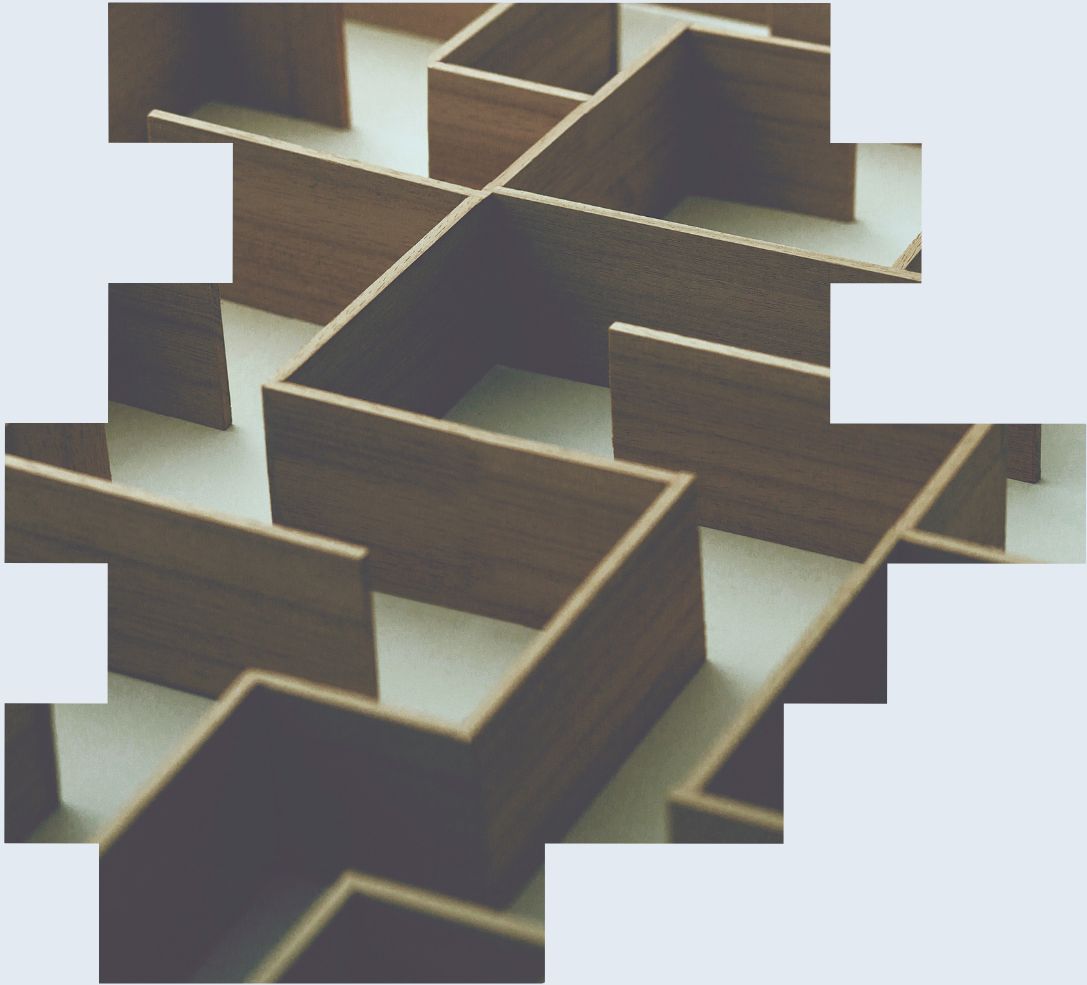
Encirc Beverages operates in a highly dynamic FMCG environment where shift patterns have a significant impact on productivity (OEE), customer service and employee job satisfaction.
It requires the business to undertake an annual shift pattern design process that factors in seasonal fluctuating demand as well as shift worker preferences and wider operational and supply chain matters.
This was becoming an increasingly complex process to manage, with Encirc Beverages’ employee engagement survey revealing that some colleagues were becoming frustrated with their shift patterns and the shift planning approach.
Like many FMCG manufacturing and distribution businesses, Encirc Beverages faced several challenges, including:
– Aligning shift patterns to demand: Creating a resourcing model that meets variable demand but provides employees with a high degree of consistency and certainty within the underlying shift pattern. Particularly important is handling the effective transition between demand periods when operations move between four-day (low) and seven-day running (peak).
– Avoiding disruption: Minimising quick shift rotations which impact shift worker rest and preventing mid-year changes to shift patterns that impact colleagues’ home lives. Also aligning shutdowns to key periods of the year where employees typically want time off (e.g. Bank Holidays and over the Christmas and New Year period).
– Balance and fairness: Ensuring all teams and employees have rosters with an equal distribution of shift types, usable rest periods and impacted weekends.
– Engagement and timing: Ensuring adequate time and space for the Trade Union to have meaningful input into the shift pattern design process and that employees receive good notice of their shift pattern for the coming year.
Given the importance of shift patterns to operational performance and HR requirements, Encirc Beverages’ management decided to engage with experts at optashift to see how these challenges could be overcome.
The ‘How’ - A data-led, collaborative approach
Over four months optashift led an accelerated shift pattern change programme.
During this time we collaborated closely with various key stakeholders within Encirc Beverages.
This included Planning, Operations and HR teams as well as the Trade Union (Unite).
Throughout the initiative we followed our robust and proven approach to shift pattern design which focuses on…
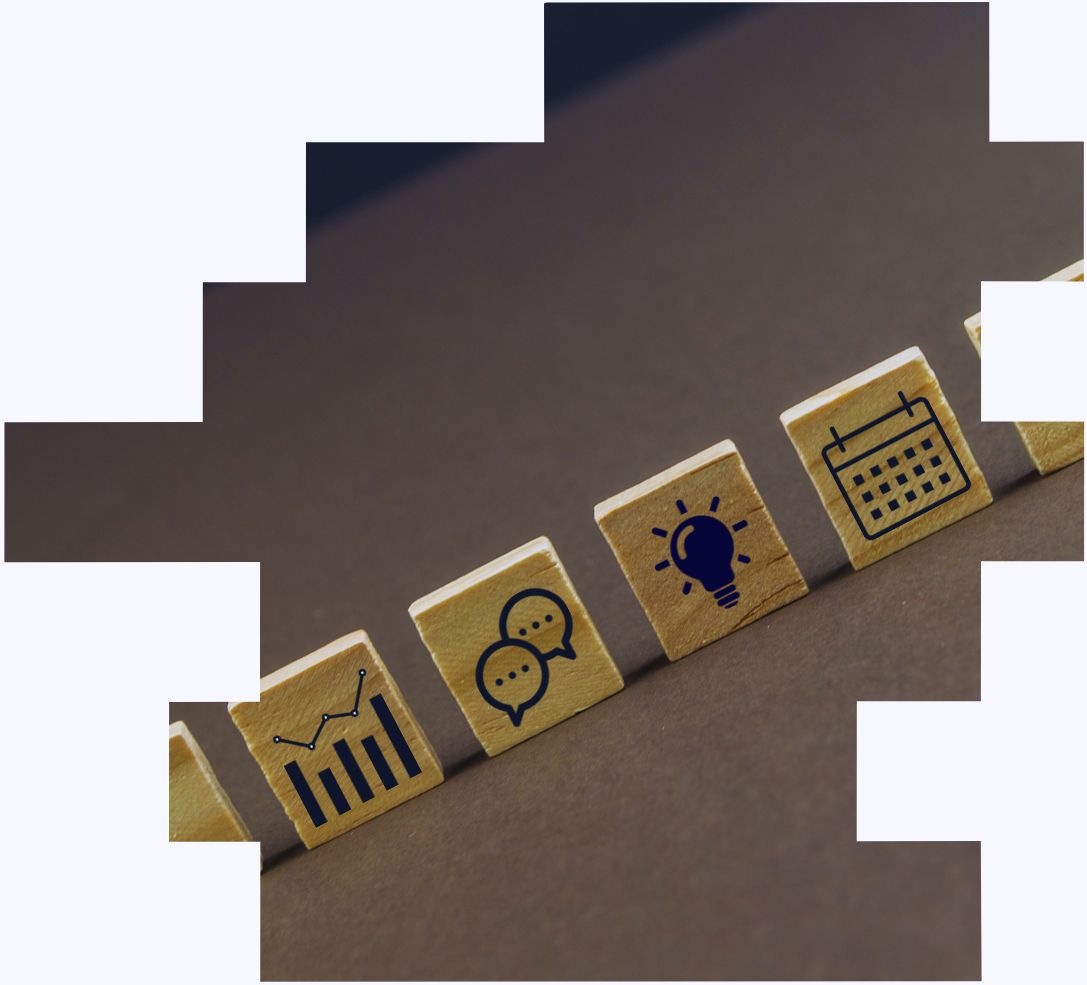
– Shift Work Analytics and Demand Planning: Undertaking detailed analysis of raw HR and operational data to understand true resourcing requirements, constraints, opportunities and how labour supply could be best aligned to demand.
– Design framework: Facilitating engagement between management and the Trade Union to openly assess current challenges, co-create rules for the shift pattern design process and define target outcomes.
– Shift Worker Preference Index: Working with the Trade Union to capture and analyse the preferences of members to guide shift pattern design and ensure the impact of the programme could be measured.
– Option exploration: Using the unique visualisation capabilities of optashift’s Plan tool, stakeholders were able to work collaboratively to design and iterate shift pattern options across multiple interactive co-creation sessions.
– Shift Calendar refinement: optashift’s interactive modelling tool was also used by our experts to view calendars for all teams across the entire year, enabling collaborative meetings where individual shifts were fine-tuned (day-by-day, week-by-week) to achieve a fair balance of shift types, weekend working and rest periods.
– Engagement and Communications: Ensuring all stakeholders remained informed and involved throughout the initiative. This included supporting the Trade Union in communicating the rationale, approach and outcomes to its members.
The Outcomes and Impact - Optimised patterns and improved relationships
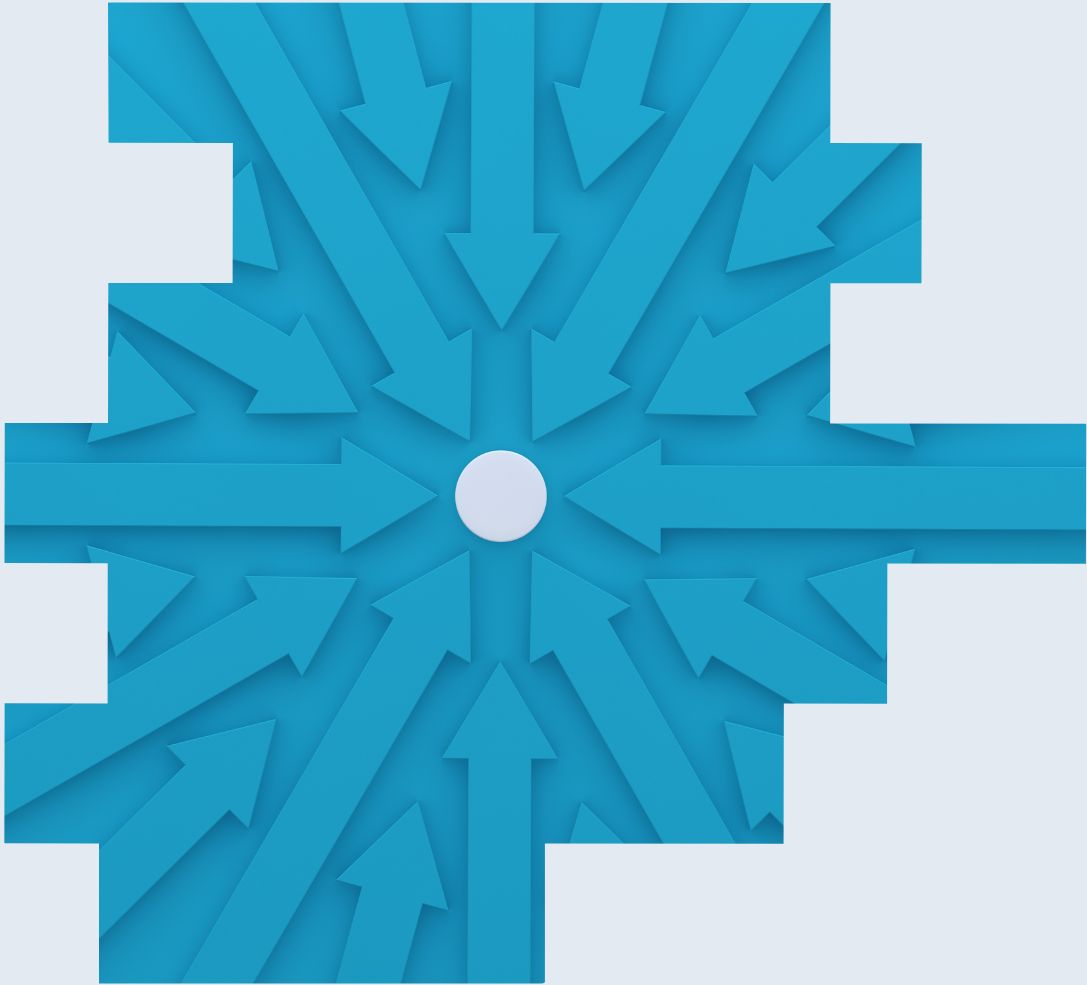
The shift pattern design process culminated in two annual shift pattern calendar options being shortlisted.
Both met demand and operational requirements and incorporated the preferences expressed by employees.
Trade Union members were then able to vote on which option they wanted, with the most popular pattern being implemented for the following year.
The shift pattern design process has delivered positive impacts for both Encirc Beverages and its shift workers…
– Operational: Aligning labour supply to demand is underpinning productivity (OEE) and cost considerations. The Planning team now have more flexibility to provide hours required by month throughout the year. Valuable management time has been freed up to focus on other areas of continuous improvement, with optashift leading on direct engagement with the Trade Union.
– Work-life balance: The new shift patterns have optimised shift rotations and reduced the number of night shifts and consecutive weekends worked. They have also increased the number of long breaks, total weekends off and ensured all employees get a minimum one week break at Easter and Christmas…and all Bank Holiday weekends fully off.
– Certainty and fairness: The annual shift pattern calendars developed provide regular, evenly distributed features with a balanced and fair distribution of shift types (days and nights), rest periods and holidays.
– Engagement and collaboration: The Shift Worker Preference Index (which enjoyed a response rate of over 90%) ensured employees have a direct say in shift pattern design. This highly engaged process received positive feedback from the Trade Union: “We genuinely feel that this has been a massive success and have enjoyed building trust and working collaboratively together.”
– Process: A new best practice approach has been embedded that will underpin year-on-year continuous improvement and support further innovation and flexibility in shift work.
The success of our data-led, co-design approach to improving shift patterns and shift work saw optashift win the Innovation and Collaboration category at Encirc Supplier Awards.
And now...? Ongoing shift work optimisation
In addition to establishing a successful new approach to shift planning, optashift is working with Encirc Beverages to improve other aspects of shift work.
This includes the wider environment and using shift work data analytics to inform continuous improvement and innovation.
If you are looking to assess your current shift patterns or want help with any aspect of shift work…contact one of our experts.
They’ll quickly help you understand more about how optimisation can help you control costs, improve productivity, secure compliance and support the wellbeing of your shift workers.
Shift Pattern, Shift Work and Shift Worker services

optashift services help you attain optimum shift work performance.
They can be delivered individually or combined to create a unified programme of continuous improvement.
Our agile approach means everything we do is tailored to your organisation and shift workers.
Shift work is complex, sensitive and always changing.
Let optashift be your trusted partner.
Our experience
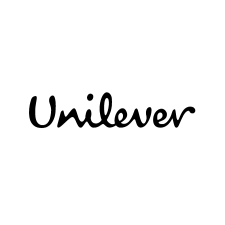
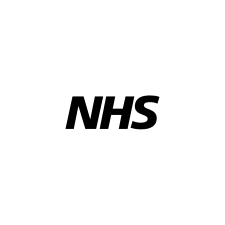
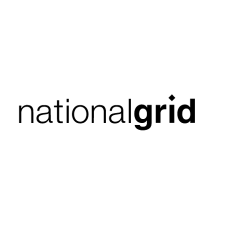
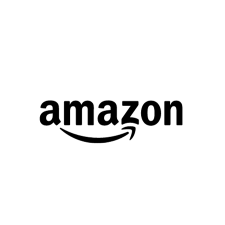
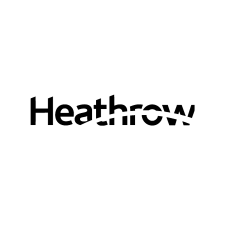
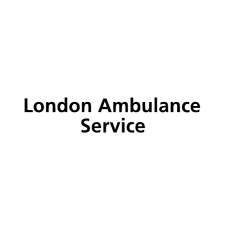
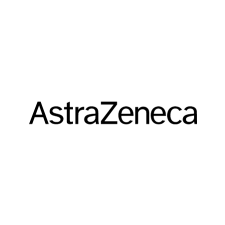
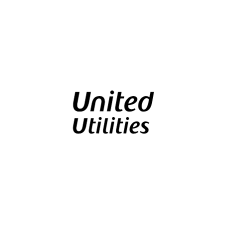
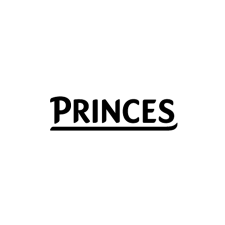
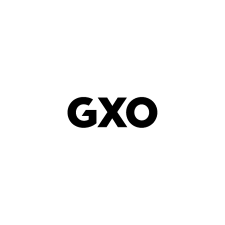
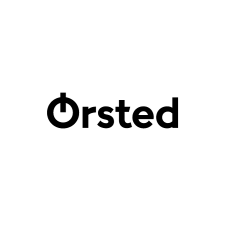
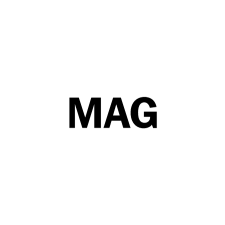