Manufacturing Shift Patterns
Shift patterns should be a key component of manufacturing planning
Manufacturing shift patterns
Businesses seeking the optimal production schedule should take a good look at whether their manufacturing shift patterns are fit for purpose.
Manufacturing shift schedules have a huge bearing on performance KPIs, impacting everything from productivity and costs to recruitment and retention.
However in many businesses manufacturing shifts are not regularly updated in line with the wider manufacturing planning process.
This risks them becoming misaligned to the requirements of the business and / or the needs of its shift workers.
Over the last 30 years our shift work experts have amassed a huge amount of sector insight by developing optimised manufacturing shift schedules to support manufacturing planning in diverse production environments.
This article briefly touches on some of the key themes relating to manufacturing shift patterns.
Operational challenges in manufacturing
Businesses are well used to the pressures of manufacturing planning and delivering an accurate manufacturing production schedule despite huge amounts of uncertainty and volatility.
Whilst every scenario is different, we see a few common operational challenges in manufacturing that relate to manufacturing shift patterns.
Some of this stems from the optimisation of manufacturing shift schedules not always being included as a key component in manufacturing planning.
Consequently businesses manufacturing shift patterns often remain the same and do not adapt to changing demand (both across the year and year-in-year out).
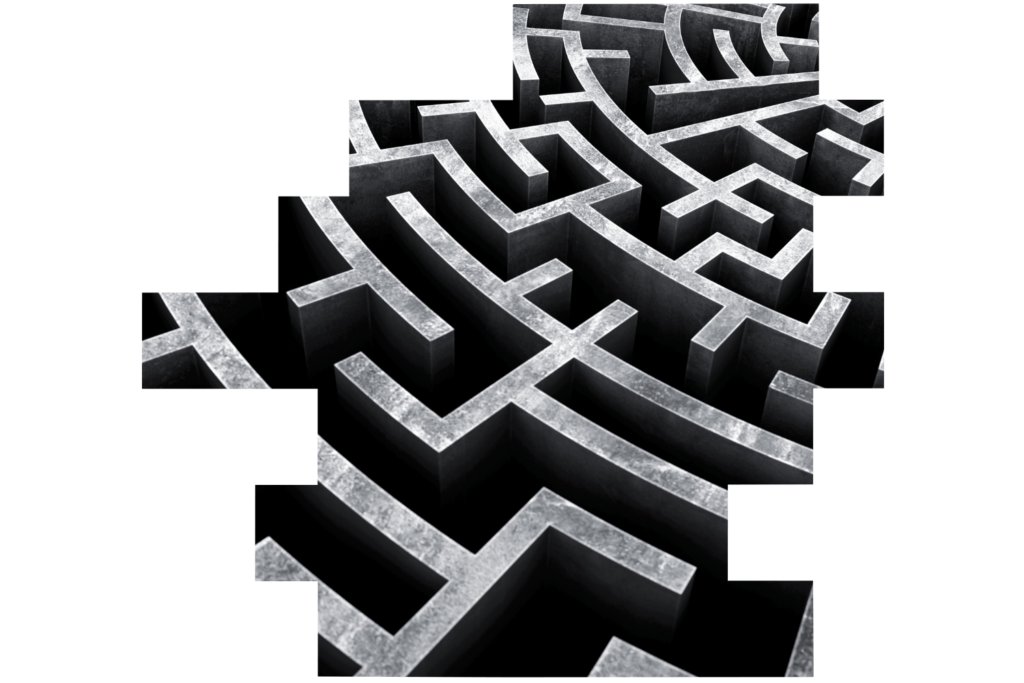
Demand volatility can be created by a wide range of factors including seasonality, orders made at short notice, un-anticipated peaks driven by customer behaviour and issues within the supply chain.
When manufacturing shift schedules provide little flexibility in how labour supply can be deployed to meet this demand, then we frequently see operational challenges in manufacturing such as:
- Lower levels of productivity, throughput and OEE as production schedules are restricted by the availability of shift worker resource or manufacturing planning options are constrained by inappropriate shift patterns
- Higher costs created by the use of overtime and agency workers used to plug the gap between capacity and demand
- A reliance on shift worker goodwill and agency labour to meet production schedules
- Negative impacts on shift worker health and morale from short notice cover requests outside the core manufacturing shift schedule
- Increased risk around breaches of shift work regulations (including the Working Time Regulations) and shift work fatigue created by long hours working and poor manufacturing shift pattern rotations
- Employee and industrial relations issues created by a lack of balance or fairness in how the manufacturing shift schedule is designed and managed
- Recruitment and retention issues created by manufacturing shift patterns that do not suit or appeal to a wide range of demographics
These operational challenges in manufacturing are not intractable. They can often be improved or resolved by designing and implementing manufacturing shift patterns that better balance supply, demand and the preferences of your shift workers.
The key is to see manufacturing shift patterns as a core component in manufacturing planning.
Shift Work Assessment
Optimising shift patterns and shift work delivers huge benefits…but complexity and competing priorities sees many organisations leave things as they are.
Our Shift Work Assessment is a streamlined process which quickly analyses all relevant operational and HR factors to give you a tailored plan for immediate improvement.
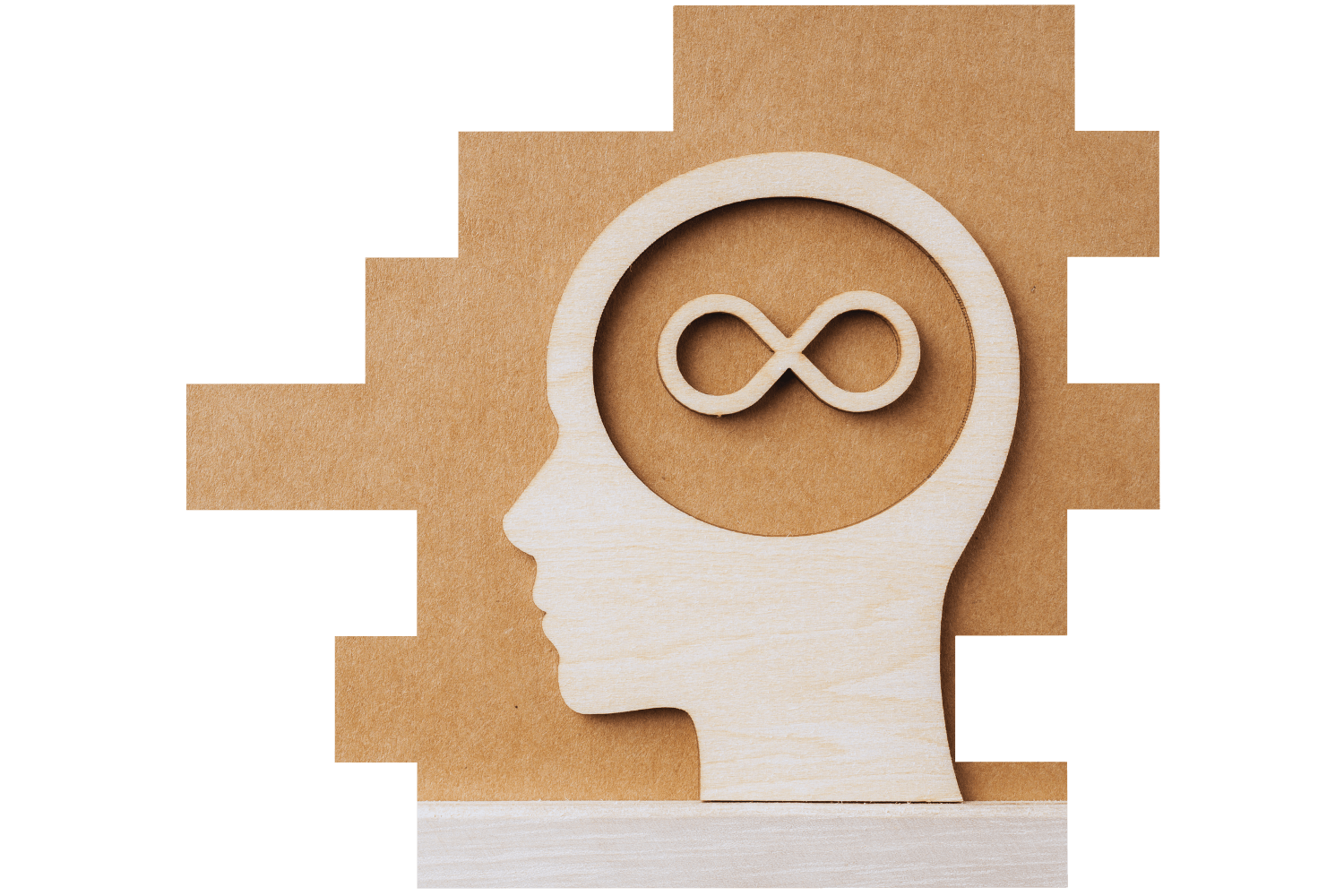
Manufacturing talent shortage
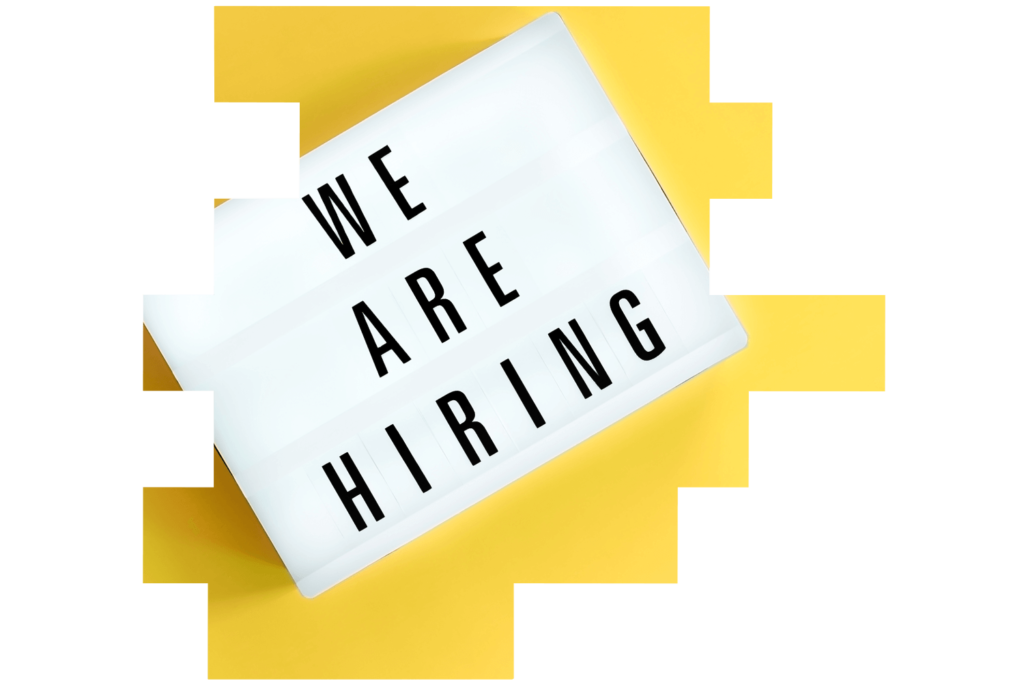
Like so many industries, manufacturing’s talent shortage is creating production capacity planning challenges.
This is especially true with more workers choosing early retirement or different careers.
Whilst there’s no easy solution to the issue, creating flexible, appealing and resilient manufacturing shift schedules can help alleviate some of the pressure.
Manufacturing shift patterns can play a crucial role in avoiding the ‘skills cliff’ by supporting skills cycling, upskilling and cross-skilling.
They can also help tackle high absence rates and retention issues by minimising overtime and long-hours working which are often key contributors to production schedule issues.
You can also broaden your potential labour pool by designing manufacturing shift patterns that appeal to the diverse requirements of a multi-generational workforce with different and evolving work-life balance needs and aspirations.
This also supports retention as you can offer employees more choice and flexibility as their personal circumstances change.
The manufacturing talent shortage will not be solved by shift patterns alone, but they are important to ensure your production schedules are not hindered by gaps in availability or skills.
Manufacturing shift patterns and demand and capacity planning
Manufacturing planning has become increasingly sophisticated and capable of creating forecasts from which to create optimal production schedules.
Detailed manufacturing demand planning and production capacity planning can be used to underpin manufacturing shift schedules that closely track demand variability throughout the day, week, month and year.
Forecasting labour demand provides the basis to create manufacturing shift patterns that better respond to short, medium and long term factors affecting production schedules.
The production capacity within core contracted hours can be maximised by ensuring they are deployed when they are required, drastically reducing the need for overtime or contingent labour support.
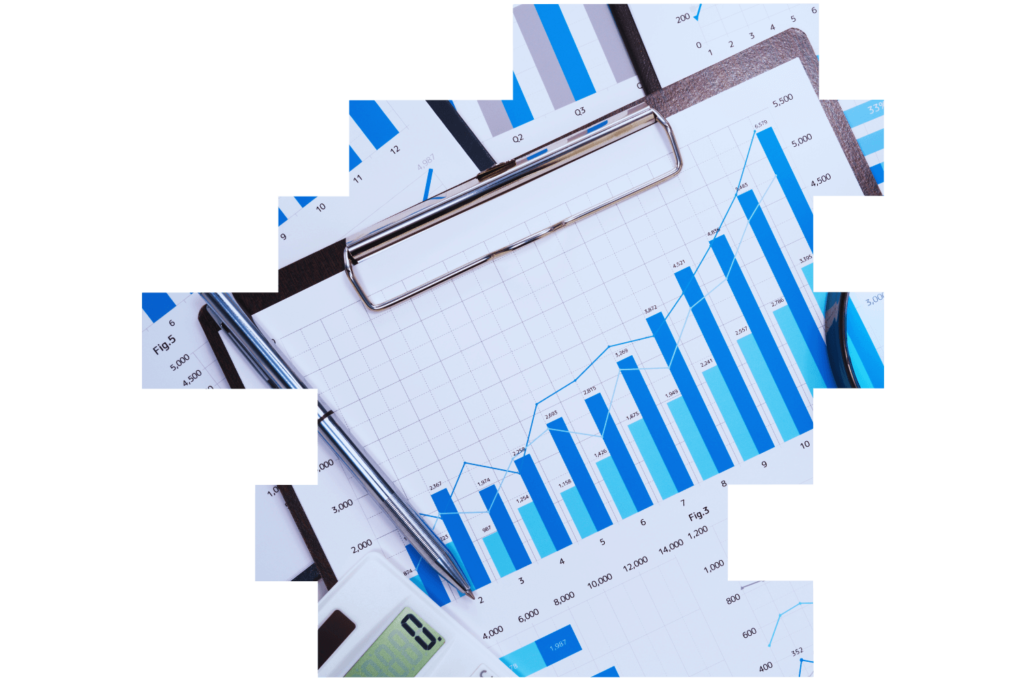
To achieve a fully optimal production schedule it’s vital that the manufacturing capacity planning process creates an accurate picture of true labour supply.
We’ve seen numerous examples where oversights can lead to significant capacity shortages, often at periods of maximum demand.
These include:
- Insufficient labour availability delivered within the base shift pattern resulting in additional costs or missed deadlines
- Stock building with significant working capital cost implications
- Labour supply limitations such as holidays, training and sickness not being considered
- The optimal skills and cover mix within a manufacturing shift is not factored in (for example in covering breaks)
Ultimately manufacturing shift schedules should be responsive to manufacturing planning.
They should provide the ability to flex up and down to support production schedules without negatively impacting your employees’ work-life balance.
Creating more flexible manufacturing shift patterns is the key to delivering optimal production schedules and having mechanisms available to respond and adapt to change.
Designing manufacturing shift patterns
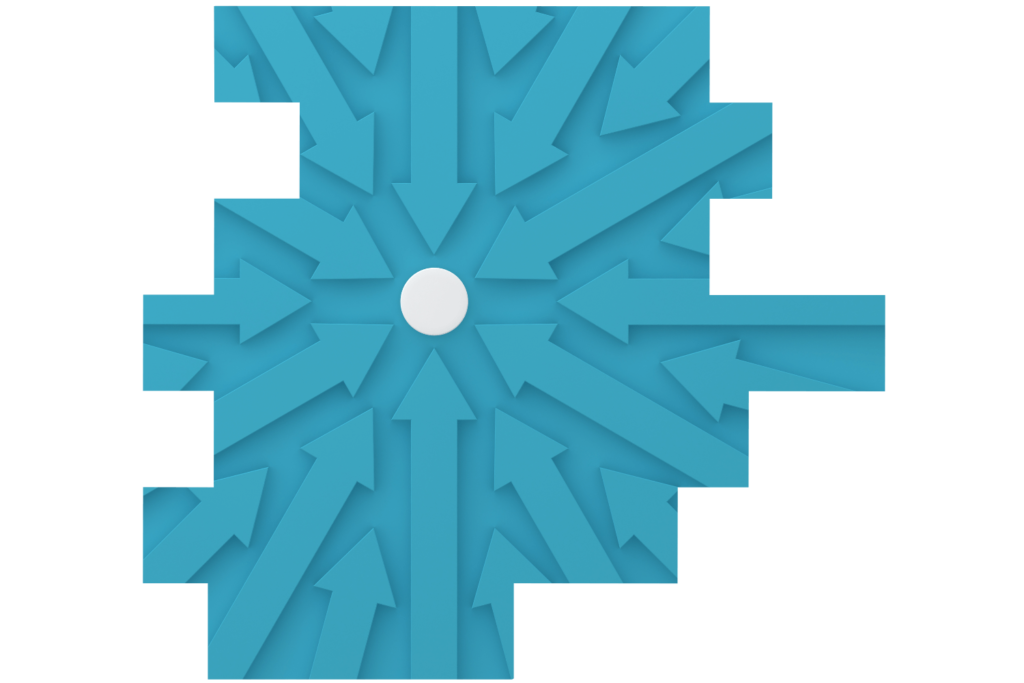
We believe that a best practice approach to designing manufacturing shift patterns should be a key part of manufacturing planning.
Assessing your current ways of working will help identify opportunities to better balance supply and demand for the benefit of your performance and people.
The process of shift pattern design is covered in a bit more detail elsewhere on this site
For manufacturing shift schedules it’s worth considering a few key pointers:
- Maximise the potential output and value of contracted hours by deploying them in line with manufacturing demand planning and production capacity planning
- Consider targeting alternative working hours on your most productive assets and / or solutions like 10-day fortnights to maximise changeover efficiency
- Target the removal of embedded overtime, particularly if it fundamental to production schedules and is reliant on goodwill
- Ensure agency labour use is not normalised and instead is used more precisely to providing cover for low-skilled requirements, long-term absence and emergencies. This will reduce the overhead and management burden associated with securing and onboarding contingent labour
- Aim to increase certainty and fairness around flexible mechanisms like bank hours and on-call. Use effective shift planning techniques to provide shift workers with a good understanding of when they might be needed and fair advanced warning of when they will need to cover a shift
- Distribute less popular manufacturing shifts equitably across the workforce. These could be night shifts, weekend working or on-call shifts
- Create manufacturing shift patterns that provide usable leisure time. Avoid shifts that might break up extended leave periods and provision for popular times of the year such as summer
Shift Patterns
Finding shift patterns that balance the needs of your organisation and shift workers can be a slow and painful process.
optashift’s Shift Pattern Design service combines data science, expert insight and collaboration to create shift patterns that are fully optimised for your performance and people.
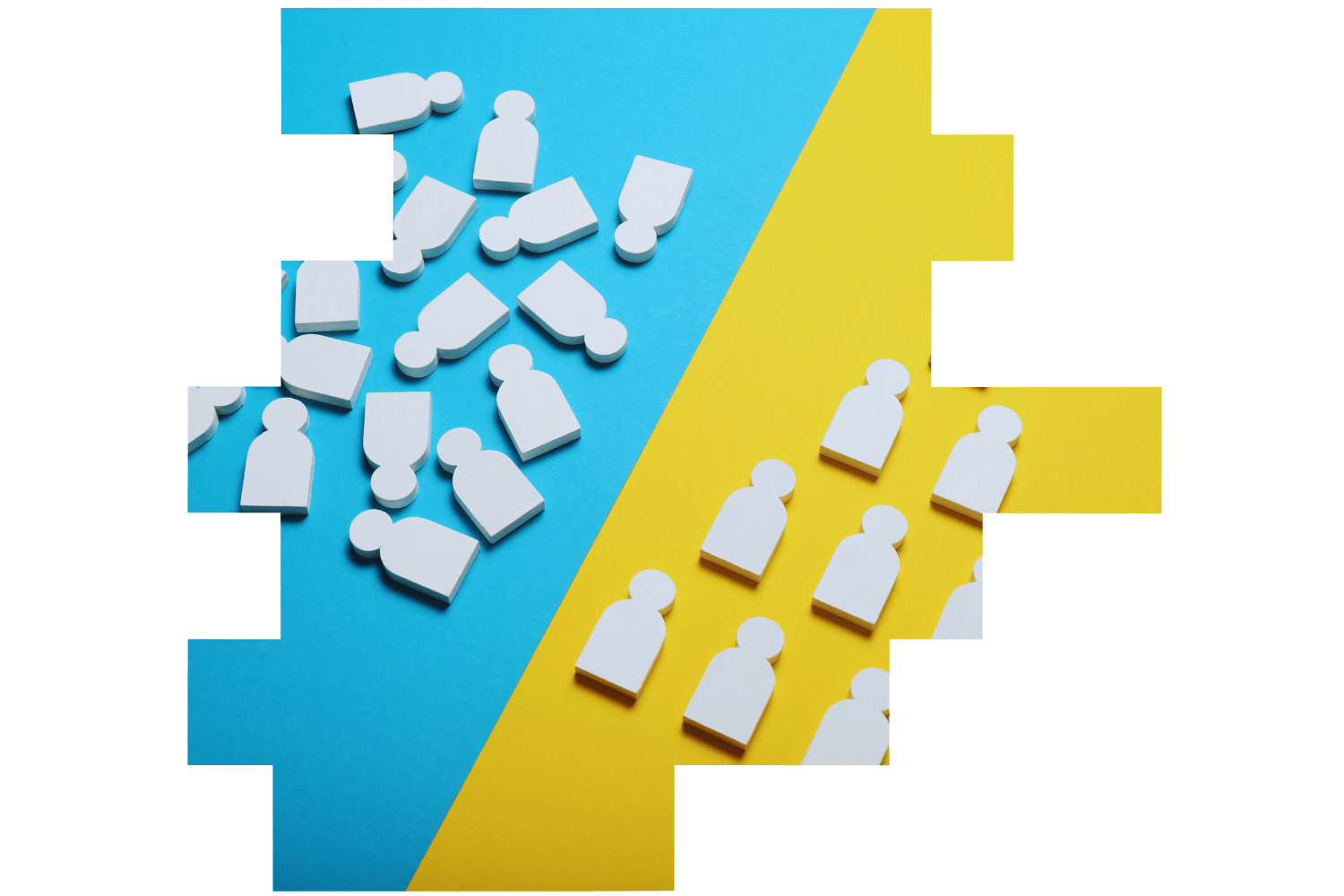
Employee engagement in manufacturing
Employee engagement in manufacturing is crucial to the process of changing shift patterns.
Regardless of how inefficient or unpopular your current manufacturing shift patterns may be, attempting to change them can be strongly opposed by the workforce.
Sometimes this resistance stems from a negative fallout from previous attempts to better align shift patterns with production schedules.
Other times it can be because of natural fear of the unknown and the direct impact manufacturing shift patterns have on peoples personal lives.
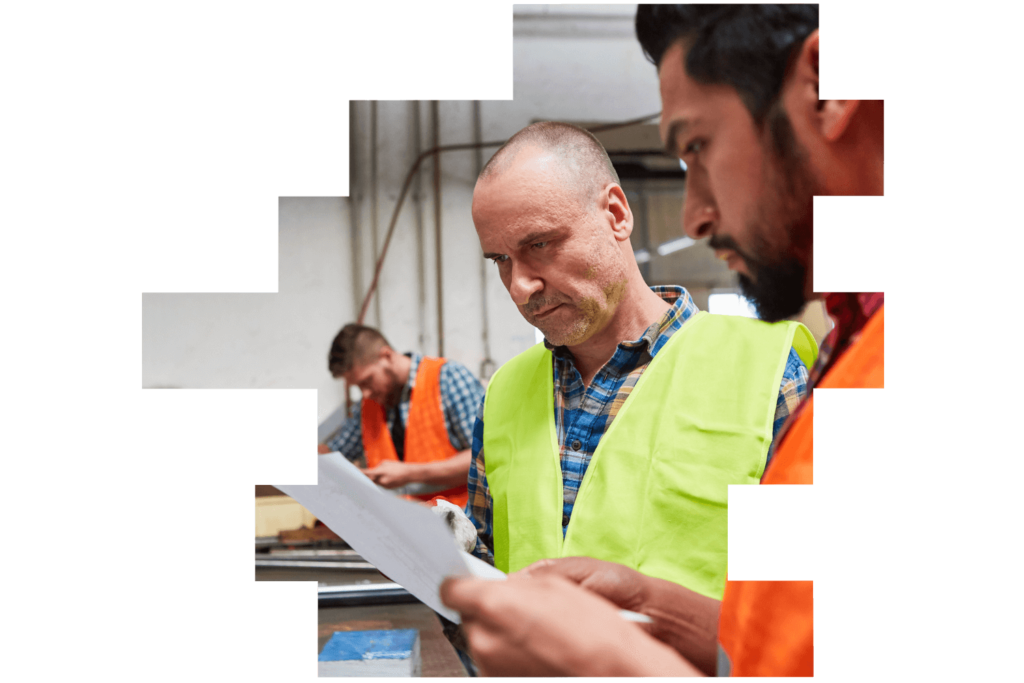
Designing new manufacturing shift schedules in isolation and imposing them on a workforce with little collaboration is often the cause of employee relations issues and industrial unrest.
It makes employee engagement in manufacturing vital to delivering the necessary change.
The opportunity exists to take a collaborative approach, working with shift workers and Trade Unions to create new manufacturing shift schedules.
For example, as part of manufacturing planning you can:
- Establish a process of engagement that is clear and has the buy-in of all stakeholders
- Ensure you understand shift worker sentiment regarding current manufacturing shifts. What are they unhappy about? What do they feel could be done better?
- Explain the need for change and the benefits it will bring in terms of productivity, job security and flexibility
- Collaborate directly with shift workers to design new manufacturing shift patterns that balance manufacturing planning and production schedule requirements with shift worker preferences
Manufacturing health and safety
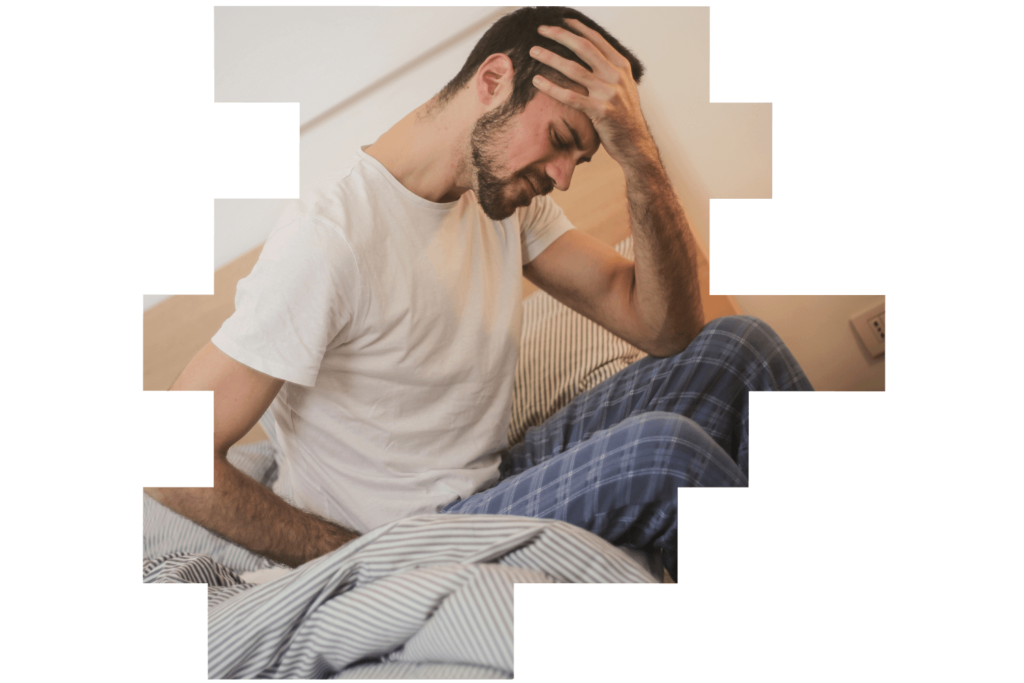
Avoiding shift work fatigue should be major consideration in both manufacturing planning and manufacturing health and safety strategies.
Shift patterns are central to this, so it’s vital all your manufacturing shift schedules are appraised using a fatigue and risk index.
You should also have a shift work policy that proactively manages risk and provides mechanisms to identify and address potential issues.
Fatigue risk can be reduced by creating manufacturing shift patterns that reduce long hours working, overtime and sub-optimal shift rotations.
How this is achieved is a huge topic that we’ll cover in more detail in separate articles.
It’s worth noting that in addition to compliance with shift work regulations, minimising overworking helps reduce absence and create a more healthy, positive working environment.
Manufacturing shift schedules that actively protect shift worker health and wellbeing are key to both production schedules and effective recruitment and retention strategies.
Tackle Shift Work Fatigue
Shift work fatigue can have a dramatic impact on health and safety, shift worker wellbeing and productivity.
optashift will work with you to develop a sophisticated Fatigue Risk Management System tailored to your organisation and workforce.
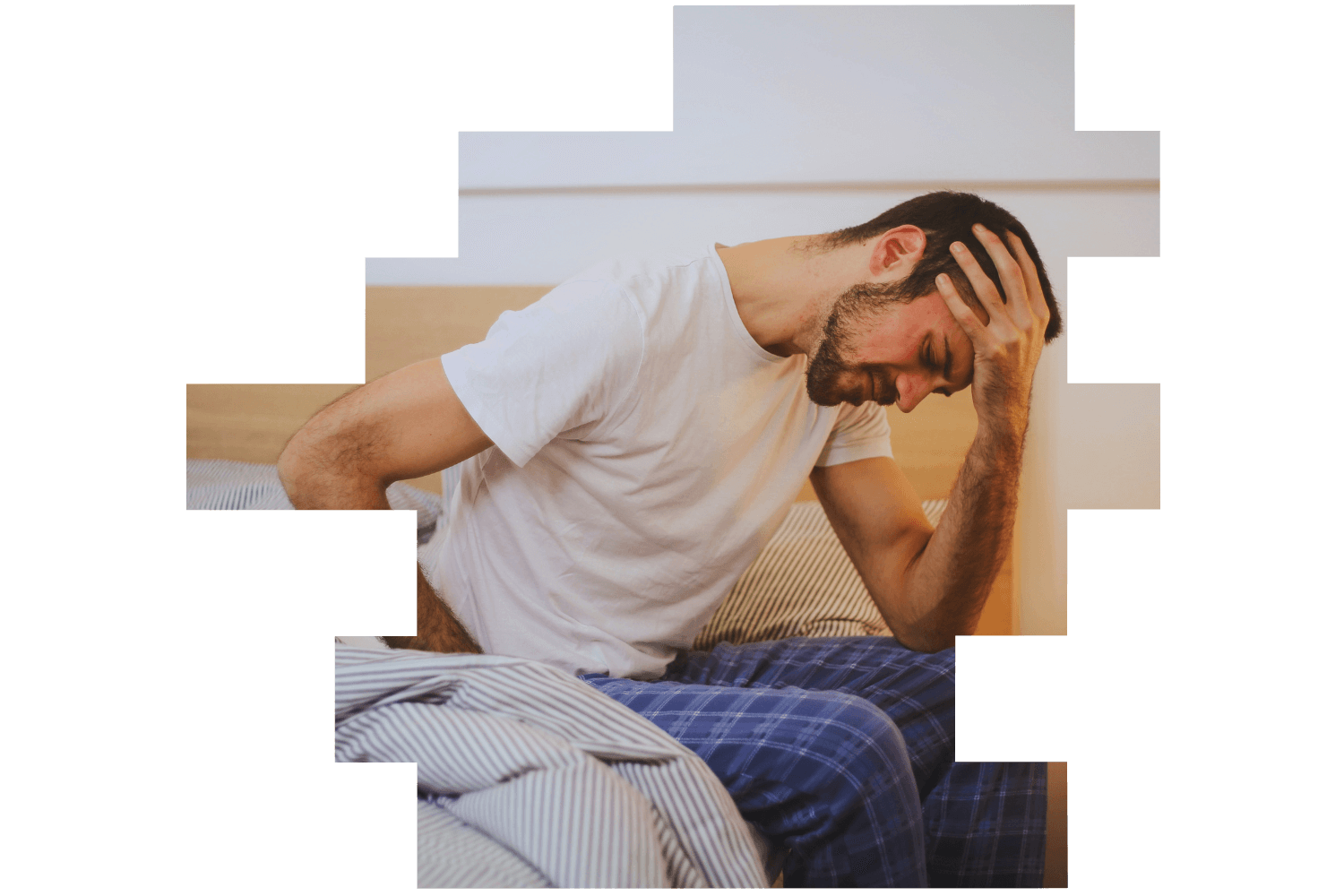
Manufacturing workforce management
A big component in success of manufacturing shift patterns is whether they are managed using robust shift work policy and manufacturing workforce management (WFM) software.
You may have the most efficient and popular manufacturing shift patterns possible, but things can quickly unravel if they are not managed and maintained effectively.
It’s worth considering a few aspects here…
Both supply and demand will change so it is key to have a system that will identify this and automate the management of such situations.
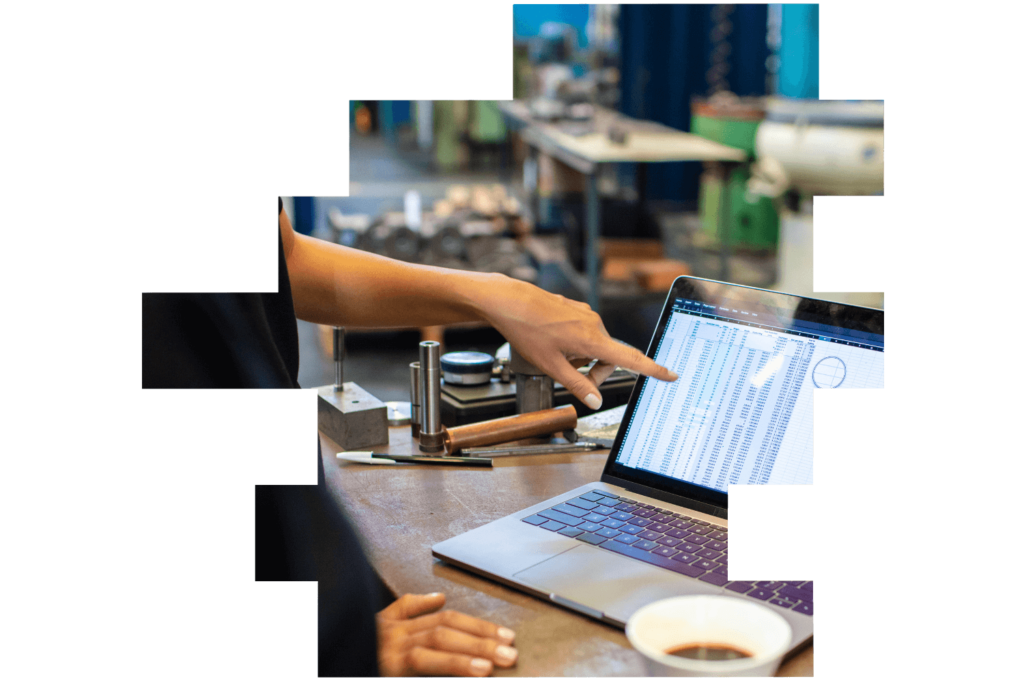
Also make sure your system is effectively monitoring hours worked to avoid costly payroll errors, compliance breaches and employee relations issues.
It’s crucial any manufacturing workforce management software is capable and configured to handle the complexity of rotating shift patterns and daily rostering requirements (like shift swaps, seasonal patterns, flexible working patterns, holiday booking and absence management).
Check you can extract valuable workforce analytics data so you can analyse the performance of manufacturing shift schedules and use the data to feed into manufacturing planning and drive continuous improvement.
Help with manufacturing shift patterns
This article barely scratched the surface when it comes to the importance of manufacturing shift schedules to manufacturing planning, production schedules and recruitment and retention.
If you are looking for help with manufacturing shift patterns or manufacturing shift schedule examples then get in touch.
optashift experts have been working with manufacturers for nearly 40 years and can provide valuable support as you look to improve manufacturing planning and optimise production schedules.
Our approach combines data and collaboration to deliver transformative benefits across food and beverage, pharmaceutical, general manufacturing and print and packaging.
Our experience
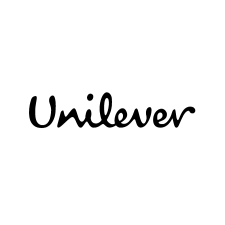
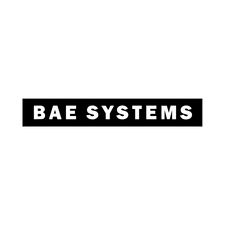
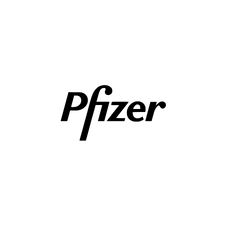
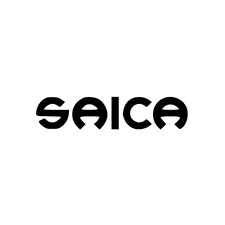
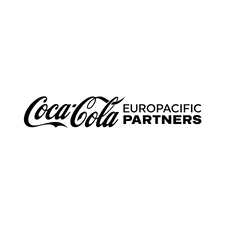
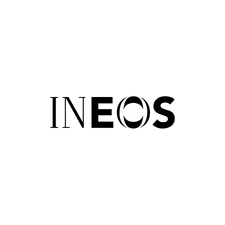
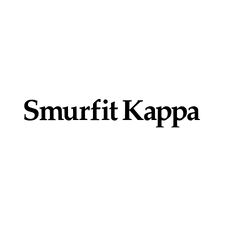
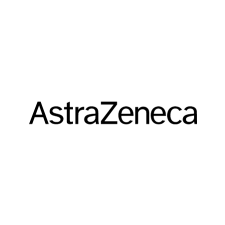
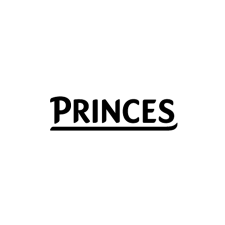
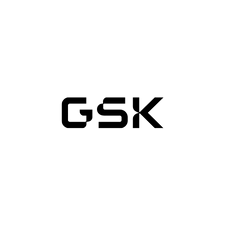
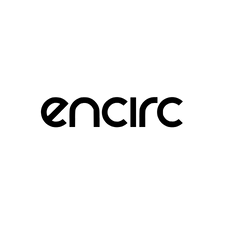
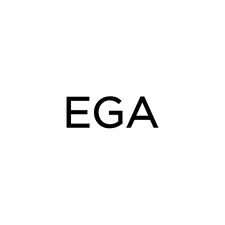
Shift Pattern, Shift Work and Shift Worker services
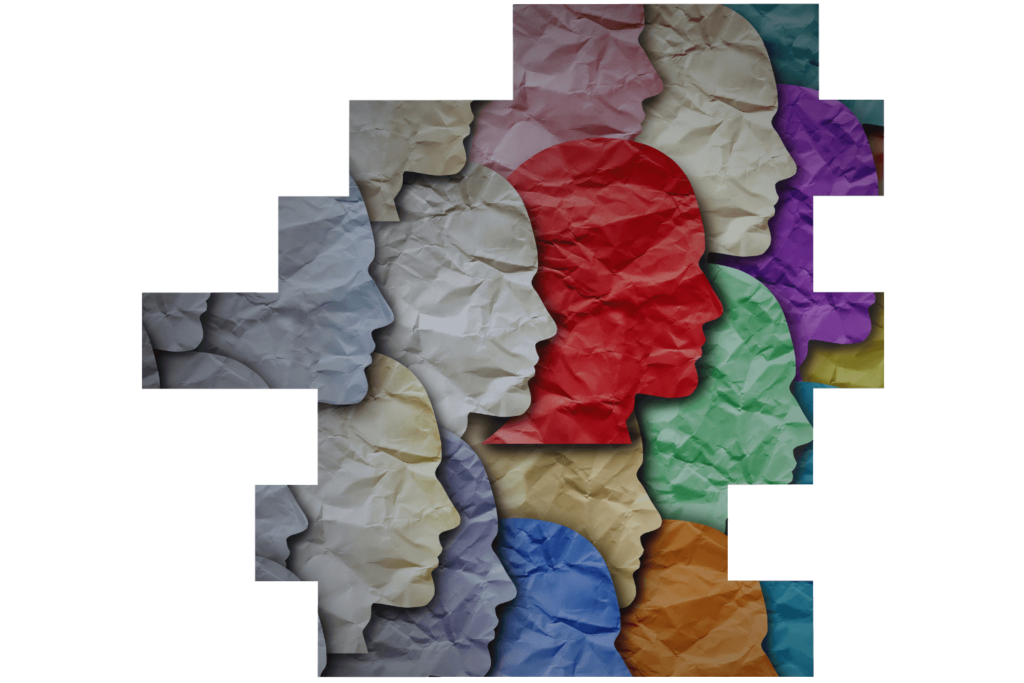
optashift services help you attain optimum shift work performance.
They can be delivered individually or combined to create a unified programme of continuous improvement.
Our agile approach means everything we do is tailored to your organisation and shift workers.
Shift work is complex, sensitive and always changing.
Let optashift be your trusted partner.